Stressproof® Facts
A list of facts for Stressproof®
The Grade 1144 Modified
Grade AISI 1144 was developed by the LaSalle Steel Company back in the mid 1930s, for the sole purpose of creating the Stressproof® product.
The Patent
The original patent for the steel product and method of manufacture was based on cold drawing and heavy drafts.
This was followed by the highest temperature stress relieving treatment possible in order to obtain a combination of the properties:
Strength, Wear Resistance, Minimum Warpage, Excellent Machinability
High Temperature Stress Relieving
The goal of high temperature stress relieving was to obtain maximum ductility while having minimum warpage and excellent machinability. The stress relieving temperature selection is based on 60 years of experience and thorough documentation.
The goal of high temperature stress relieving was to obtain maximum ductility while having minimum warpage and excellent machinability. The stress relieving temperature selection is based on 60 years of experience and thorough documentation.
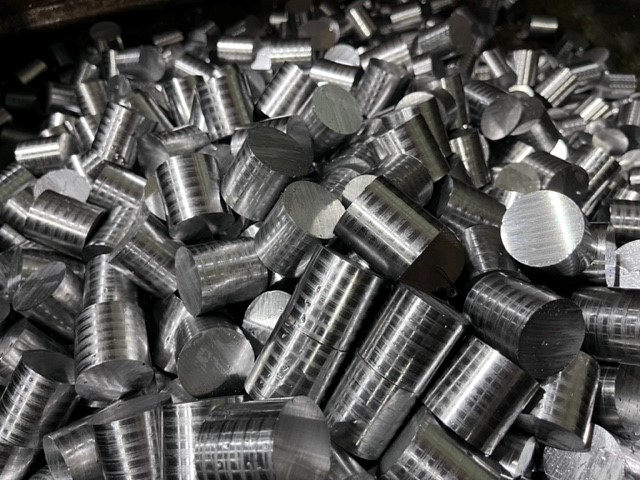
Drawing Dies
Niagara LaSalle’s proprietary drawing dies are a critical component to the production of Stressproof®.
A warpage test is always performed on the first bar drawing through either a new or reground die. Warpage tests are also regularly made as a standard quality assurance procedure. The results are then a part of the quality assurance program.
Surface Quality
Magnetic or roto bar testing for seams on every order is part of the Stressproof® manufacturing process.
To further improve quality, Niagara LaSalle reduced the standard seam depth tolerance for Stressproof® from 0.0015 per each 1/16″ to 0.0010 per each 1/16″.
This results in a savings of 3% in material weight purchased.
ASTM A311 Specification
This specification was written in an attempt to cover Stressproof® properties.
It covers multiple grades and numerous conditions of stress-relieved cold drawn bars in order to meet minimum mechanical property requirements.
Mechanical Property Testing
A minimum of one test (tensile, yield, elongation, R/A) is made for every 50,000lbs or less.
Mechanical property testing is always the final operation after all processing has been completed.